Custom Metal Stamping Process of Spring Contacts
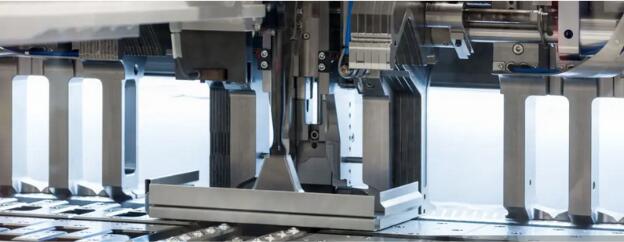
Proprietary Die Design
JCL engineers employ extensive simulation and analysis to develop state-of-the-art progressive stamping dies customized for the spring contact geometries and material properties. This enables precise execution of complex forming for custom metal stamping.
Automated Metal Preparation Lines
Custom coils and strips of high conductivity alloys like beryllium copper, phosphor bronze undergo automated cut-to-length blanking or reel-to-reel processing as preparation for high efficiency stamping operations.
High-Speed Precision
JCL operates advanced progressive stamping presses, including 1000 metric ton capacity, enabling tailored contact blanks through precision stamping processes with forces exceeding 100,000 psi for property enhancement.
Secondary Processing
Formed spring contact blanks are further processed in inline or standalone systems to achieve final shapes like coils, loops, torsion springs, cantilevers through secondary stamping steps.
Finishing and Terminal Crimping
Back-end robotic automation enables deburring, electropolishing, crimping, testing and quality analysis to finish contacts post stamping operations for connector integration with capacities scaled to high volumes.
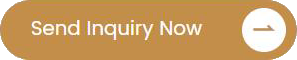
Major Advantages of Stamped Spring Contacts
Complex Geometries
As mentioned previously, stamping enables intricate contact shapes impractical through other manufacturing approaches. This empowers connector designs for challenging applications.
High Production Efficiency
The progressive stamping process allows very rapid production of spring contacts once the dies are ready. Quality consistency across millions of contacts enables cost-efficient mass manufacturing.
Property Control
Stamping induces favorable compressive stresses up to 100,000 psi to transform properties. This augments electrical connectivity and mechanical reliability of the spring contacts over other methods.
Miniaturization Capabilities
Precision progressive stamping can fabricate remarkably small, reliable contact springs. It can achieve thin walls, tight tolerances and microscale features difficult otherwise, enabling miniaturized connectors.
Design Flexibility
In addition to 3D forming, secondary operations like bending, twisting, crimping, punching enable diverse spring contact types like coils, torsion springs, cantilevers, and customizable interface geometries.
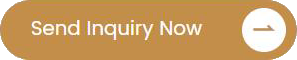
Different Application Areas Of Stamped Spring Contacts
Electronic Connectors
Stamped spring contacts excel in electronic interconnects, from oxidation-resistant gold-plated pins in desktop computer and device ports to high-speed, high-frequency contacts in automotive control systems and precision instruments. Their resilience handles 1000s of insertion cycles.
Battery Management Systems
Stamped lithium-ion battery connectors integrate formed beryllium copper alloy spring contacts. The reactive-element spring properties maintain constant pressure accommodating cell stack expansion-contraction to improve battery pack safety, thermal performance, and electrical conduction over life cycles.
Power Transmission and Distribution
Robust power connectors employed in high voltage AC-DC industrial and utility grids utilize special alloys like Incoloy and conductive composites. The materials and progressive forming provide anti-corrosion contact springs conducting over 1000 amperes under extreme temperatures, stresses for decades.
Automotive Systems
Stamped terminals and connectors are ubiquitous in vehicles for signal and power transfer in constrained, high temperature environments. Contacts in engine control modules, transmission devices, hybrid circuits withstand vibration, fuels, oils over lifetimes owing to stamping alloys and resilience.
Consumer Devices
Miniature connectors with stamped cantilever, coil or torsion spring contacts reliably interconnect displays, sensors, logic boards, accessories in smartphones and portable electronics. The contacts maintain low-resistance connections despite frequent use thanks to resilient conductive alloys and intricate forming.
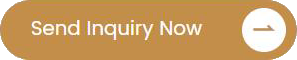
Why Choose JCL for Custom Metal Stamping Spring Contacts
Innovative Stamping Process
We have in house expert employees who can handle the spring contacts stamping process skillfully. With that we will have innovative machinery to conduct the whole process in our factory. Through our stamping presses and tools, our team can stamp spring contacts to any shape or size.
Unique Spring Design
At JCL we have engineers who are capable of designing unique spring contacts. They understand how material thickness, coil shape and number can affect the performance of spring contacts. Our engineers make sure that everything aligns with the design so it can perform well. Before starting the manufacturing, our team tests the design if it is functional or not for the particular application.
Advanced Plating System
We also have an advanced plating system to coat your spring contacts. We have electroplating lines that we use to apply layers of tin, gold or other materials in our spring contacts. Through our plating system we ensure that we apply a consistent thick material in all of our spring contacts.
Quality Control
Manufacturing quality spring contacts for our customers is our top priority. To ensure we manufacture quality products for you, we use an automated vision inspection system. With that we also conduct electrical and mechanical testing to ensure that our spring contacts will perform according to our customers expectation.
Rapid Prototyping
We know how much the right design matters for your metal spring contact. For this reason we give our customers the option for rapid prototyping and design irritation. We will create the prototype sample and send it to you for your approval. We will fine tune the spring design contacts until it's satisfy you. Our team will start the manufacturing process only after having your approval.