Design and Planning
JCD sheet metal fabrication manufacturer talks with customers to understand their requirements first. Our engineers then design and plan everything about the speaker mesh - including hole patterns, size, materials, thickness and finishes. We make tailored stamping dies to fulfill the custom specifications.
Piercing
Metal Piercing is the most vital step in the speaker mesh metal stamping process. Here we punch the customized hole patterns into the metal sheet using automated precision stamping machines.
We prefer doing hole-by-hole piercing over all holes together. In this method, we will create a one-by-one hole through metal piercing. And will repeat the process until the entire pattern is formed on the metal sheet.
Our machines pierce with immense perpendicular pressure to stamp out clean, accurately placed holes of the specified diameters.
Here is a table detailing key aspects of our precision piercing process for speaker meshes:
Parameter | Guidelines | Reasoning |
Minimum Hole Diameter | ≥ 20% greater than metal sheet thickness <br> ≥ 2 x for stainless steel sheets | Ensures clean hole punching without excessive material distortions |
Minimum Hole Spacing | ≥ 2 x metal sheet thickness | Prevents hole distortions and maintains accuracy in hole positions |
Hole Layout | Staggered pattern, not all holes together | Avoid distortions in high hole density designs |
Piercing Pressure | High tonnage perpendicular force | Achieves dimensional precision in hole diameters |
Hole Position Tolerance | ± 0.1 mm | Maintains precision alignment crucial for sound quality |
Design Clearances | Extra spacing for slots <10x and >10x sheet thickness <br> Added gap from bends | Avoids slot and hole distortions during speaker mesh shaping |
We adjust the piercing approach depending on material type, hole sizes, shape and quantity to optimize mesh consistency.
Forming
The perforated metal sheet then goes through forming rolls and presses to shape the mesh into required enclosures like cones, squares, grilles etc. The mesh carefully goes through the forming step to avoid strains around the hole patterns.
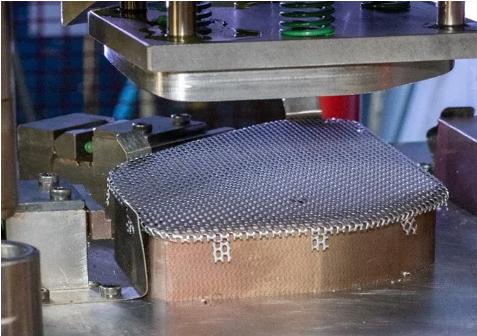
Finishing
After that, we will apply speciality coatings and finishes based on requirements - matte paint, gloss enamels, anodized colors, chrome plate etc. This will increase the aesthetics and long-term durability of your speaker mesh.
Quality Checks
The finished metal speaker mesh finally goes through rigorous quality testing to validate hole consistency, positioning precision, and adhesion of coatings and to verify that it meets your requirements and the quality standard.
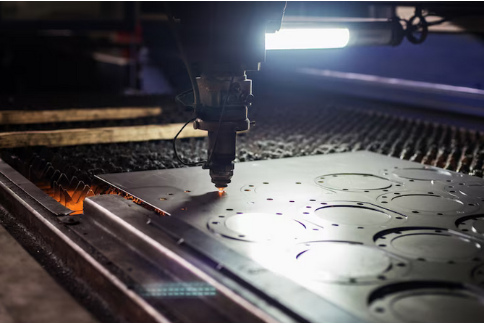
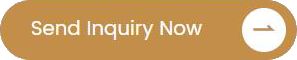