JCL’s Custom Metal Stamping Process for Electrical Bracket Boxes
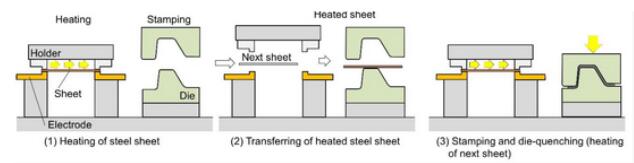
Coil Sheet Payoff
First, Large 10-ton coils of thin 22 gauge mild steel are loaded onto powered decoiler machines that feed sheet steel stock into the progressive stamping press at 5 feet per minute. These decoilers help to unwind the steel coils, feeding the sheet steel stock into the progressive stamping press at a rate of 5 feet per minute.
Feed Mechanism Alignment
Then we drive the electric servo to adjust the linear feed rate of the steel band through the indexing die stations to ensure the accuracy of punch alignment. This meticulous adjustment is also critical for the precision of the subsequent stamping process.
Pilot Pinhole Punching
Our initial metal stamping station has a set of tapered guide pins that punch small pilot indexing holes into both edges of the steel band. These holes work as downstream registration references, assisting in the alignment of subsequent custom metal stamping processes.
Profile Blank Shearing
In our next station, we have a set of custom-machined medium carbon steel profile knives. We use these precision-ground knives to cut the overall rectangular outline shape of the electrical box panels along the steel band edges as the metal stamping process progresses. In this stage, we define the basic shape of the electrical bracket box.
Mounting Hardware Forming
Moving further with the progressive die tooling, we also use eccentric cams with hardened inserts. By using these tools, we cold-form threaded nut receptacles, ground screw holes, and mount bolt holes according to the specified design requirements in the passing perform strip.
Conduit Knockout Piercing
After that, our team will use punches and die blocks designed to remove 1/2" and 3/4" diameter slugs from the panels. It will create conduit and cable access knockout ports at marked intervals within the defined electrical bracket box profile.
Flange Bending
Subsequent forming station dies are employed to bend the side flanges of the trailing electrical bracket box walls to 90 degrees. This bending operation gives the enclosure its distinctive box frame shape.
Profile Part Chop Off
At the final piercing dies trim the excess material and cut the fully formed steel frame box section pieces from the steel band. We eject the finished electrical bracket box performance from the last station of the press line, completing the custom metal stamping process.
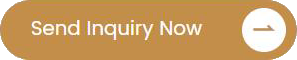
Key Benefits of Jcl's Electrical Bracket Boxes
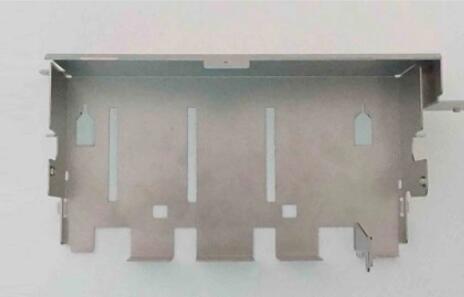
Custom Engineered Designs
JCL's electrical bracket boxes are custom-engineered based on your specific requirements. It can vary in size, shape, finish, and functionality. Our expert team uses the latest modeling software to manufacture customized bracket boxes tailored to fit the electrical application.
Durability & Strength
Our precision manufacturing from aluminum and steel alloys results in robust and durable electrical bracket boxes that give lasting protection and structural integrity in demanding electrical settings. The materials and thicknesses are decided depending on the required mechanical strength specifications.
Corrosion Resistant
Our electrical bracket boxes feature finishes including powder coating, anodizing, nickel plating, or stainless steel materials selected to withstand corrosion. All configurations are designed for outdoor, humid, coastal, or chemical plant environments.
Code Compliance
Our engineering team makes sure that bracket boxes meet essential electrical standards for spacing, fastening points, conduit openings, and ingress protection. They accommodate required internal component layouts. Design adaptability facilitates global electrical certification compliance.
Cost Effectiveness
Compared to field-constructed alternatives, JCL's electrical bracket boxes provide a cost-effective solution with quicker turnaround times. Our automated production methods allow high volume capacity for large orders.
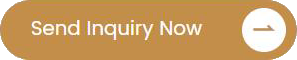